CentriPipe MN DOT Stormwater
MN DOT recently conducted tests of a new pipe rehabilitation solution called centrifugally cast concrete pipe, also known as CCCP or CentriPipe. Using equipment and engineered mortar provided by APM Permaform, District 6 relined 80 feet of badly deteriorated 36-inch corrugated metal pipe (CMP). The pipe was severely rusted, with holes in the floor and an interior section of 33-inch pipe that had separated.
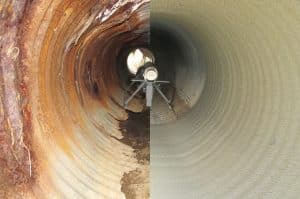
CCCP uses a spinning nozzle, inserted into pipe and retracted by a winch, to spray mortar onto pipe interiors. By varying the retraction speed and spin rate, very precise thicknesses can be applied. If fiber-reinforced engineered mortar is used, the result is a smooth, structurally sound inner pipe. Because the new pipe is bonded to the original steel or concrete pipe and needs to be only a few inches thick, pipe diameter isn’t significantly reduced.
CCCP isn’t exactly new; it’s been used in manhole restoration since the mid-1990s and is now widely accepted for that purpose. Chicago, for example, is using CCCP and engineered mortar to systematically rehabilitate all of the city’s deteriorating brick manholes. But using CCCP in horizontal pipe is new; initial testing and results are promising and should result in greatly expanded use of CCCP. When used in horizontal pipe, the spin caster is pulled through the pipe on a skid. In the MN DOT test pipe, after cleaning, the CMP floor was so uneven that some mortar had to be laid to provide a smooth skidding surface. The mortar used is mixed on site and includes high-density polypropylene reinforcing fibers and other additives. It can be sprayed, cast, or gravity-flowed, and progresses to final set in as little as four hours. For this test, two passes were made on successive days, laying down a 3/4-inch layer of mortar each time, plus a final pass with a curing compound. Each pass took less than two hours, and after the first pass some spot repairs were made to fill voids caused by deteriorated pipe invert. The final result was, essentially, a new, smooth, structurally sound, 1 1/2-inch thick concrete pipe, bonded with the original CMP.
Costing information currently relies on estimates, because CCCP has not yet seen large-scale use on horizontal pipe. But preliminary estimates suggest that costs per foot will be somewhere between that of HDPE and CIPP, at least in smaller-diameter pipe. For larger diameter pipe, cost per foot is likely to be significantly less than CIPP.
This was a challenging test project due to badly deteriorated pipe, shallow depth that exposes the pipe to freeze/thaw cycles, and heavy loading from farm equipment. Initial results are good and CentriPipe’s combination of cost effectiveness, reasonable staging area requirements, and minimal pipe diameter reduction is very promising.